I started experimenting with natural dyeing in 2019 and quickly became fascinated with the colours that can be obtained from plants, especially since many of them are considered weeds! For me there is great satisfaction in knowing that the wool and the dye has come off the same land, it connects me to the land, nature and to the past.
Living on top of a windy hill in Shetland means that plants are much more limited than the UK mainland and are much later in growing due to the weather conditions. The local plants I have been using are rhubarb, dock, dandelions, nettles and others that often crofters try to get rid of! Most often the shades that are obtained from these plants are yellow so I use modifiers, dried plants and plant extracts to create a wider colour palette.
I dye everything on a small scale in large pots generally in ten skeins at a time. It’s a time-consuming process; enough plant material needs to be obtained and then I usually pour over boiling water and leave the plant material to steep at least over night or a few days. The next day the material is simmered in the steeping water for an hour, left to cool and again left overnight or for several days and it is often simmered again to release more dye depending on the material. The plant material is removed from the pot and prepared yarn is added to the pot and heated, then left to cool and often left overnight yet again. Natural dyeing is a slow process and certainly not one that can be rushed, it can take several days or even weeks to dye one batch of yarn!


Natural dyes are extremely sensitive to temperature, pH and the presence of other elements, so it can be hard to replicate colours. Plants vary in pigment depending on the growing seasons and conditions and where they are grown, so the colour obtained from plants taken from different areas can vary. The dye obtained from a plant early in the year may be quite different to the dye obtained later in the same year even though it has been growing in the same place. I like the fact that each batch is slightly different, and colours can be obtained by using what is available at the time, there is something magical about waiting to see what colours will come out of the dye pot.
Before dyeing, depending on the dye material used, I treat the yarn with a mordant (usually Alum or Rhubarb leaf) which in simple terms ensures the dye will chemically attach to the yarn. The yarn is rinsed well after dyeing but to make sure there is no colour run, especially when making a garment with more than one shade such as a Fair Isle design, it is recommenced the yarn is rinsed in lukewarm water before use and hung up to dry. If you are going to be knitting an item with more than one colour it is advisable to knit a swatch using those colours and wash the swatch warm water and a pH neural soap before rinsing and drying to check that there is no colour run. I would advise avoiding soaking your work just in case.
Because natural dyes are so sensitive to pH it is important to use only a pH neutral soap. Something specially designed for washing wool is ideal. Avoid using vinegar in the washing water, vinegar is often recommended for helping to fix dyes, but it will not work for naturally dyed yarn and will probably shift the colour entirely!
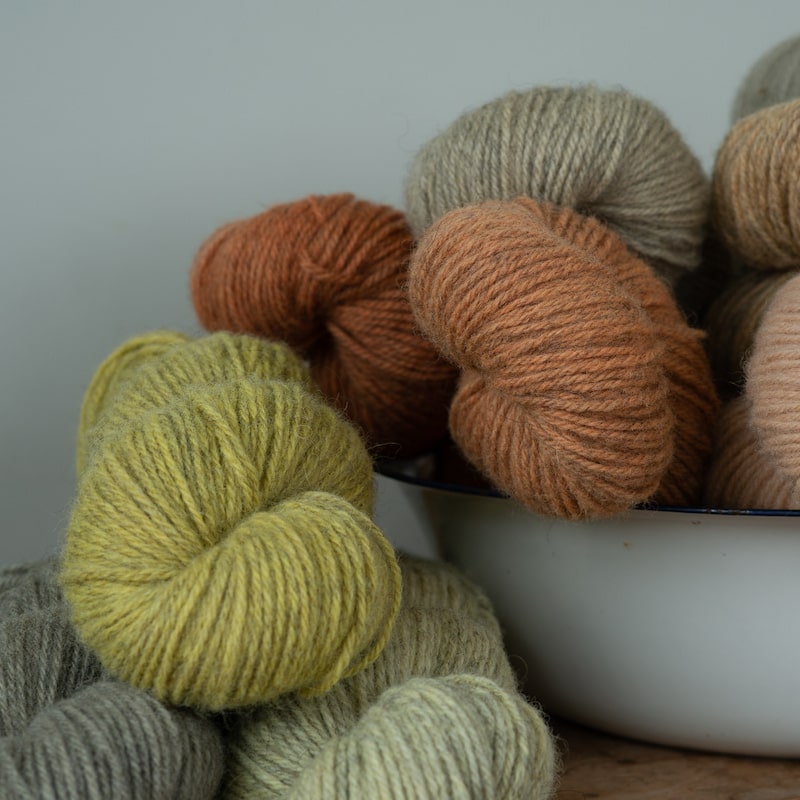
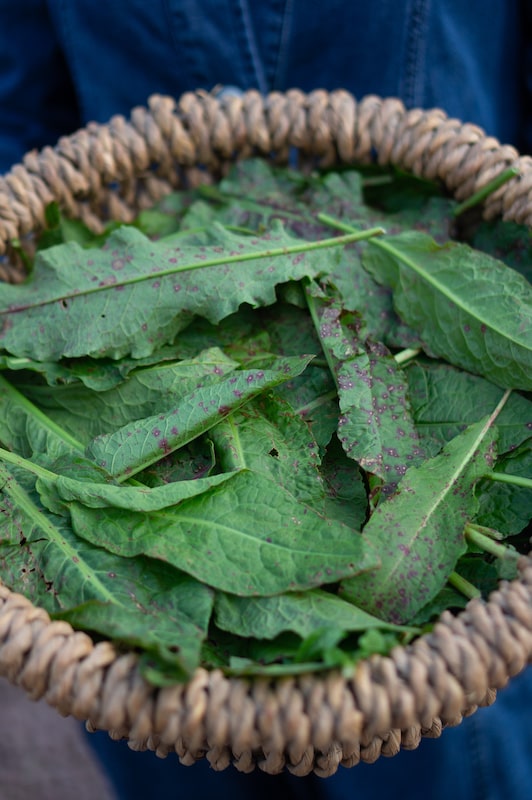
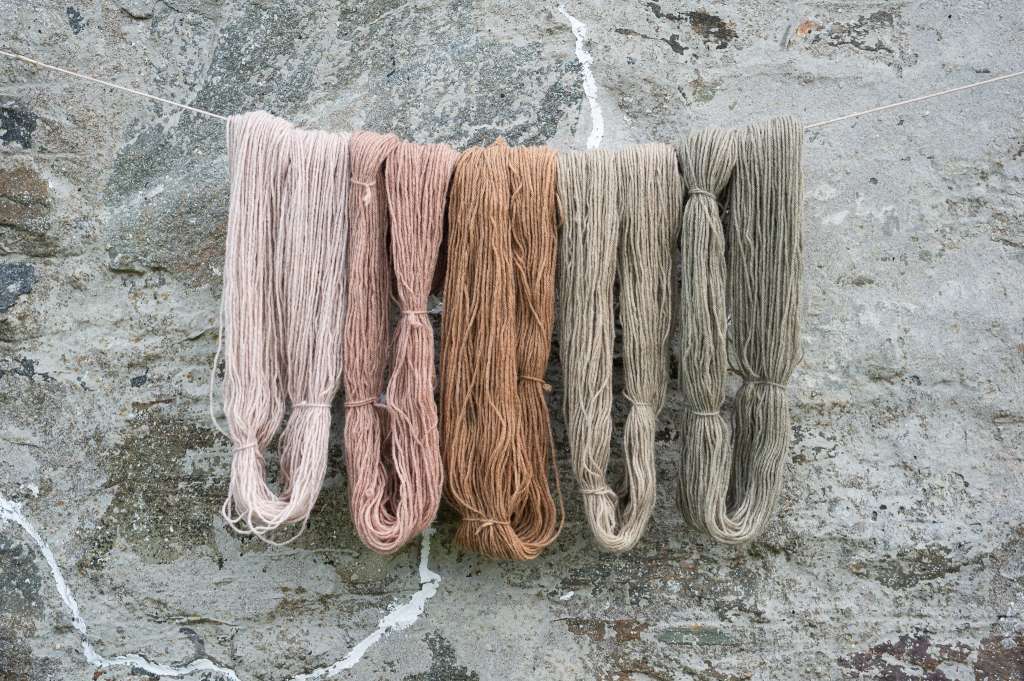
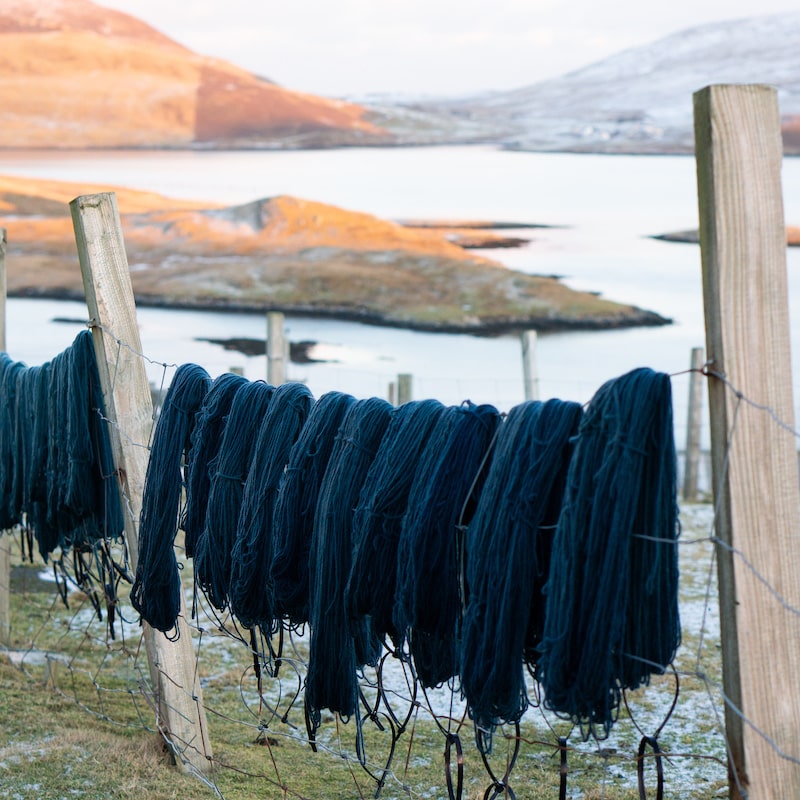

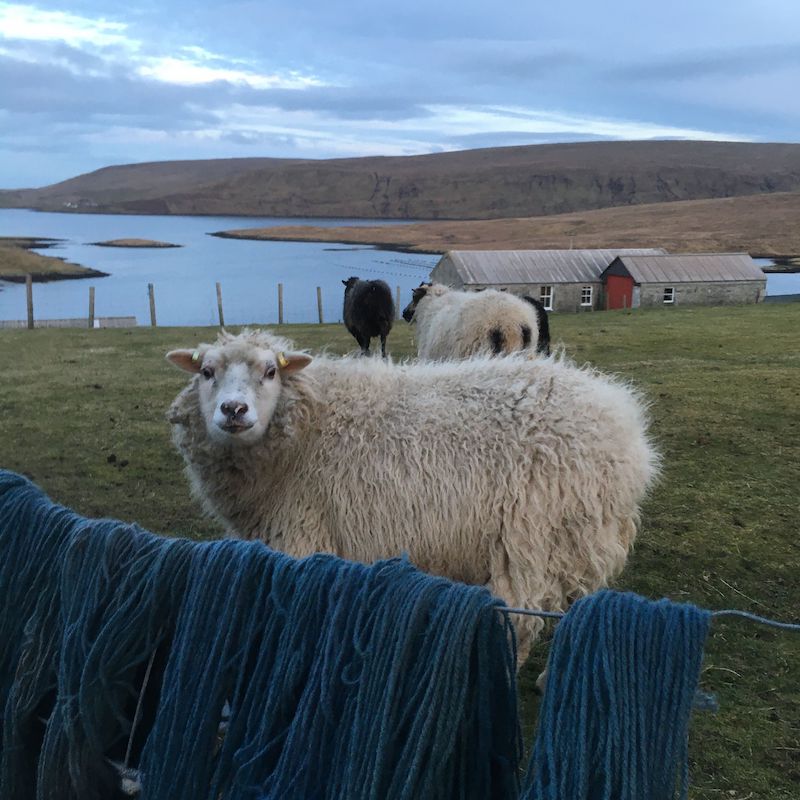